




2024 WINNERS
Your Gateway to Recognition and Success!
​
A fantastic night of prestige, celebration, and inspiration at the Awards Evening for Africa Supply Chain Excellence. This event is a testament to the spirit of innovation that propels Africa's supply chain profession forward.
-
81 entries were received this year
-
50 entries reached the presentation judging stage at which the entrants presented online to the judges.
-
33 Finalists were chosen from the 50 entries
View the Photos from the 2024 Awards Dinner
2024 Sponsors & Partners
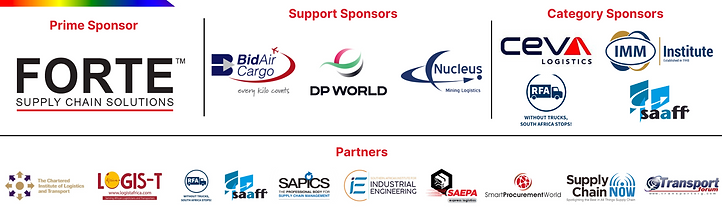
Judges Spotlight Award for Supply Chain Excellence

The Luke Commission powered by Luvelo
The Luke Commission (TLC) is an NGO delivering compassionate, comprehensive healthcare to the most isolated and underserved people of Eswatini, hosting over 300,000 patient visits annually. Powered by the Luvelo software designed by TLC, it is home to a world class medical facility called the Miracle Hub and Eswatini’s first oxygen plant, crucial for local supply and global standards compliance, especially given oxygen shortages during the COVID-19 pandemic. This was built by the Luke Commission in a remarkable 52 days to cope with the 3rd wave of the covid pandemic when there was no oxygen available from neighbouring South Africa. With renewable energy prioritised due to electricity cuts, the launch of a medical drone network, and a custom-built digital platform to ensure visible and efficient supply chains, TLC is innovating to maximise health and development in Eswatini. The Judges Spotlight Award recognized that supply chains save lives and celebrates and supports The Luke Commission’s formidable impact and resilience in the face of adversity.
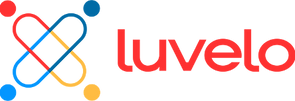

Demand Planning & Management
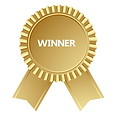

BCE Food Equipment
Managing evolving supply chain landscapes BCE, a key player in Sub-Saharan Africa’s hospitality and food service industries, navigated complex supply chain challenges exacerbated by the COVID-19 pandemic, geopolitical tensions, and global economic conditions. The disruptions significantly strained supplier capacities, led to raw material shortages, and escalated costs while making customer demand highly unpredictable. BCE responded by aligning its procurement strategies with the “new normal,” aiming not only to maintain but enhance service levels amidst heightened competition. In 2017, BCE proactively engaged b2Wise to implement Demand-Driven Material Requirements Planning (DDMRP). Initially utilising an Excel-based model and later dedicated software, DDMRP proved pivotal during the pandemic’s onset. It enabled BCE to swiftly manage critical purchase orders, optimise cash flow, and demonstrate agility in supply chain operations. Facing challenges within its procurement department during the “Great Resignation”, BCE restructured and appointed a manager aligned with DDMRP principles. This leadership change facilitated seamless integration of DDMRP across operations. Strategic initiatives focused on optimising working capital, refining customer service, and streamlining processes were prioritised under new leadership. Product ranges were reviewed, spare methodologies revised, and supplier relationships optimised to counter rising costs and enhance competitiveness. Investments in workforce training and streamlined processes bolstered efficiency and agility. Role reallocations and automation upgrades further improved responsiveness and customer service, ensuring BCE’s readiness for sustained success amid evolving supply chain landscapes. With robust structures, methodologies, and leadership in place, BCE is well-positioned to support SMEs in creating jobs in South Africa’s dynamic market.
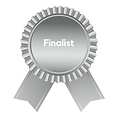

USAID GHSC-PSM, AFYA UGAVI ACTIVITY IN KENYA, CHEMONICS INTERNATIONAL
Building Self-Reliant Supply Chains through Strong Governance Systems: the Case of Kenya Governance structures, including policies, regulations, strategies, and oversight, empower local supply chain actors to operate efficiently, establishing clear roles and accountability. This is crucial as countries transition from donor funding to independent management of lifesaving health commodities. In Kenya, the devolved governance system between the national level and 47 county governments created challenges for supply chain coordination. Before 2019, Kenya’s MoH Division of Health Products and Medical Technologies (DHPT) lacked a cohesive strategy for coordinating health commodities, leading to inefficiency and wastage. Counties faced fragmentation in supply chain functions such as quantification, procurement, storage, warehousing, and training. To address these challenges, Chemonics, through the USAID GHSC-PSM Afya Ugavi (AU) Activity, partnered with Kenya’s MoH to empower local actors to manage their health supply chain independently of donor support. AU supported the DHPT in establishing Kenya’s first-ever Health Products and Technologies Supply Chain Strategy 2020– 2025. This strategy created Health Products and Technologies Units (HPTUs) to coordinate supply chain activities at the sub-national level. HPTUs now serve as coordinating bodies for supply chain activities within counties and with the national DHPT and have been established in all 47 counties. AU helped develop standard guidelines, provided infrastructure for offices, led organizational capacity assessments and supply chain audits, conducted supportive supervision and data use trainings, and assisted in forecasting and quantification exercises. As a result, counties have taken ownership of supply chain management functions, advocating for increased domestic resource allocation for commodities and performing order quantification and reporting independently, greatly reducing stockout rates for lifesaving health commodities.
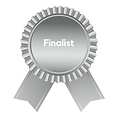

USAID GHSC-PSM IN ZAMBIA, CHEMONICS INTERNATIONAL
Strengthening Health Supply Chain Data in Zambia Consumption Anomalies Detection (CAD) Tool In many low- and middle-income countries (LMICs), unreliable digital infrastructure leads to fragmented data systems, non-standardized identification methods, and reliance on paper-based processes. This poses challenges for minimally trained supply chain and health facility personnel in inputting data into complex systems. In addition, issues of commodity security such as spoilage, ASCEA AWARDS 2024 pilferage, stockout can pose a threat to the health commodity supply chain. In Zambia, the GHSCPSM project partnered with the MoH to combat these issues through a digital tool, the Consumption Anomalies Detection (CAD) Tool. This tool utilises historical consumption data to spot observations or trends that fall outside the normal patterns or trends -- by facility and product. To ensure sustainability and reduce reliance on donor funds, GHSC-PSM focused on close coordination with country stakeholders and comprehensive training for local staff in order to institutionalize the tool. The tool has had an impact on both improving data quality and increasing commodity security in the country. Additionally, the use of the tool has generated cost savings between $500k to $1M USD per year, through preventing commodity expiries. This streamlined approach not only addresses immediate data challenges but also lays the groundwork for longterm improvements in health supply chain management across diverse global contexts. Further, GHSC-PSM has ensured that the tool can be adapted to suit other unique country contexts, enhancing its scalability and robustness beyond its original scope.
Procurement & Supply Management
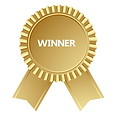

Nucleus Mining Logistics
Sustainable Procurement. Nucleus Mining Logistics was not only able to survive the “Covid years” but has been able to grow exponentially over the last 2-3 years. The organisation has more than doubled its growth. This has been as a result of outstanding service to existing customers while identifying and security new customers and providing excellent care and attention to all customers. The team at Nucleus Mining Logistics Group really cares and takes pride in the services delivered. From a small transporting company not only has the existing footprint been grown but new branches have been opened as well. The project at Alphamin Bisie Mining in the DRC saw the implementation of the procurement consolidation module. Struggling with excessive import duties and massive paperwork this implementation resulted in savings from the streamlined process as well as increasing shipments and adding team members. Environmentally this solution ensures more paperless work and demonstrates green procurement whilst ensuring energy conservation thus ensuring its sustainability.
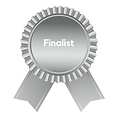

Procure
Africa
Transforming traditional procurement processes. Procure Africa believes that technology is the catalyst for transforming traditional procurement processes, and its platform serves as a testament to this conviction. As a dynamic and forwardthinking company, they have embarked on a journey to redefine how businesses connect and transact, particularly in the medium-sized business sector. This cutting-edge platform is designed to simplify and streamline procurement processes, providing a digital marketplace where buyers and suppliers can seamlessly interact. The Procure Africa platform leverages advanced technology to streamline the entire procurement lifecycle. From RFQ creation to supplier selection and transaction completion, our system ensures efficiency and transparency at every step. Procure Africa understands the importance of a reliable and diverse supplier network. This technology seamlessly integrates a vetted supplier database, ensuring that buyers have access to a wide range of trusted and high-quality suppliers. Data-Driven Decision-Making: In the realm of procurement, informed decisions are key. Combined with a User-Friendly Interface the user experience is prioritised. Beyond a mere marketplace, Procure Africa introduces innovative business models, including a credit system that incentivizes suppliers to respond to RFQs promptly. This unique approach adds an extra layer of dynamism to the platform. Their technological innovations are globally relevant, they are particularly committed to making a significant impact within the Southern African Development Community (SADC) region. This regional focus sets us apart as a company contributing to the growth and development of African businesses.
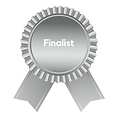

Beapo
Collaboration and Agility. When faced with urgent client demand for a batch of engines Beapo realised that a global shortage had hit the entire engine supply chain posing a threat to the success of their client’s operations and in turn the economy. Knowing the gravity of the situation, the Beapo team immediately rallied to find a solution. Transparent communication with the client ensued. The long-term partnership with the Original Equipment Manufacturer (OEM) Scania proved to be a game-changer. Through collaborative discussions, they explored the possibility of adapting an alternative Scania engine series to match the client’s requirements. It was an unconventional approach, but the prospect of delivering a tailored solution within a shorter timeframe was an opportunity worth pursuing. The engineering teams collaborated closely to adapt the engine specifications without compromising performance and reliability. This meticulous process required attention to detail and a deep understanding of both the equipment and the client’s operational needs. As the adapted equipment for the engines were put through rigorous testing, a sense of excitement and trepidation filled the air. When the results came in, they were better than expected. The engines not only met the client’s needs but also surpassed the performance of the original specifications. It was a testament to the power of innovative thinking and collaboration. What began as a shortage crisis transformed into a testament to the team’s dedication, Scania’s expertise and the power of collaborative problem solving. By thinking outside the box and prioritising our customer’s needs, Beapo not only saved a critical situation but also strengthened bonds that continue to thrive.
Manufacturing & Production Management
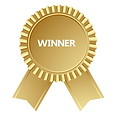
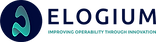
ELOGIUM
Improving Operability through Innovation. Elogium specialises in the 3D printing and localisation of spare parts. This disruptive technology is changing the face of supply chains significantly and is creating a whole new eco-system in Africa. Not only is it challenging the original equipment manufacturer (OEM) business models but it also ensures that asset utilisation is improved and prolonged. In Feb 2021 the OEM informed Elogium’s client of the discontinuation of spares for a pump. The client was faced with possible asset replacement the cost of which would be for the full range of pumps. This would result in redundant spares on the current range of pumps and a high capital cost for the replacement of them. The 3D printed super polymer impeller solution provided by Elogium saved the client significant expenditure on asset replacement. It surpassed the client’s expectations and there are now plans to adopt this in other areas of the business.
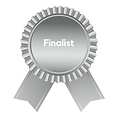
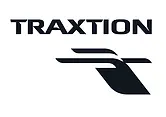
Traxtion
Innovation and Change Management: Reviving Rail Haulage Capacity. Traxtion undertook a transformative approach to revitalising rail haulage capacity using recycled General Electric (GE) U20C locomotives. Originally purchased for spare parts, these locomotives were stripped down and reimagined to meet the growing demand in the African market. Facing challenges with obsolete OEM parts, Traxtion employed strategies, leveraging local engineering firms to engineer and upgrade unavailable components. This collaboration not only facilitated locomotive rebuilds but also bolstered the local rail economy by integrating these companies into Traxtion’s supplier network for future projects. Modern control systems were implemented to enhance efficiency, while re-engineered frames and upgraded safety features like braking systems ensured compliance with contemporary standards. The result was that the first rebuilt U20C locomotive was completed in significantly less time and at a fraction of the cost compared to procuring new equivalents from an OEM. The remaining three units are due for deployment by June 2024. Throughout this initiative, Traxtion fostered supply chain enhancement, supported employee development, generated Intellectual Property, and expanded its supplier database. By repurposing aged locomotives and championing local collaboration, Traxtion has underscored its commitment to sustainability and operational efficiency, setting a precedent for future rail projects across Africa. This innovative endeavour not only ensures long-term viability for Traxtion but also supports broader efforts to optimise rail infrastructure and meet escalating transport demands effectively.
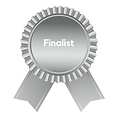

DHL Supply Chain – the impact of the X-Band System
Innovation in African Logistics DHL Supply Chain continuously strives for excellence and innovation in all operations. One such innovation is the X-Band system, which was developed to address inaccuracies in the supply sequences. These sequences, which were initially generated manually, were susceptible to human error, adversely affecting the Direct Run Rate (DRR). The initial solution to this problem saw the deployment of additional staff for pre-supply sequence verification, inadvertently escalating operational costs. However, with the implementation of the X-Band system, they have seen significant improvements including enhanced precision as the X-Band system has dramatically reduced sequence picking errors, hence improving the DRR and instilling greater confidence among customers. The system has curtailed the costs associated with rework due to incorrect supply. Also, the need for extra personnel for the verification process is now a thing of the past, further reducing our operational costs. With the X-Band system, employees can focus on one part number at a time versus reading the picking slip with all part numbers displayed, therefore simplifying the process and reducing the chance of errors. The system can detect sequence skipping and validate parts through QR code or physical part number scanning. In addition, the X-Band system introduces new functionalities, including a dashboard that displays sequence kits in progress and the systems load status. In conclusion, the X-Band system has proven invaluable in achieving goals for enhanced efficiency, cost savings, and customer satisfaction.
Inventory, Warehousing & Distribution Management
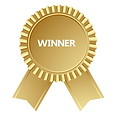
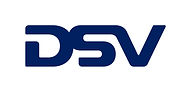
DSV
Inventory through Innovation This project highlights the importance of inventory management and what the benefits are when you have the correct stock in the correct location physically and systematically. It demonstrates what is the impact downstream and what are the potential risks if this is not in place. The project also introduces DSV’s innovative Autonomous Drone Cycle counting solution. A zero-error warehouse is no longer a luxury. Improving inventory accuracy has become an urgent mandate for big-box retailers, 3PLs, and manufacturers competing for customer loyalty. Automated inventory management system, powered by self-flying drones, addresses the challenge head on. Drones can scan inventory in the warehouse and distribution centres during nights and weekends -literally while you sleep- identifying inventory discrepancies and distilling that data into valuable insights. DSV has adopted a sustainable way in which their inventory, manhours, and resources are managed.
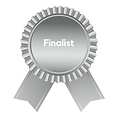
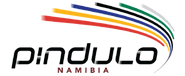
Pindulo
Namibia
Transforming the Port of Walvis Bay Pindulo Namibia has a vision to transform Walvis Bay into the pre-eminent gateway for sub- Saharan region by showcasing integrated logistics capabilities. They recently announced the news of its sixth vessel loading of copper concentrate since starting operations within the Port of Walvis Bay mid-2023. This is a monumental achievement that underscores their unwavering commitment to excellence and innovation. This isn’t just a milestone; it’s a bold statement in an industry where they began as underdogs. Their strategic approach, which focuses on creating a deep, symbiotic partnership with their clients, has not only set them apart but has catapulted them into a realm of unmatched efficiency and service. Pindulo began this journey in the face of scepticism, with numerous voices casting doubt on their lofty ambitions. Yet, as we reflect on their achievements—over 50,000 tons of bulk copper concentrate exported, a journey extending beyond 4 million kilometres (all achieved with side tippers), and a remarkable 350% surge in traditional loading speeds—the immense satisfaction felt by all at Pindulo Namibia of surpassing the expectations of sceptics is undeniable. Looking ahead, Pindulo Namibia is not just poised for another year of excellence; they are ready to redefine it. With a focus on continuous innovation, customer-centric solutions, and a relentless drive to add value, they are committed to not just meeting expectations but exceeding them.
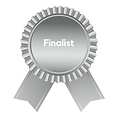

DHL Supply Chain Africa and Diageo (KBL) East Africa
Cutting-edge Solutions Revolutionising Warehouse and Transport Operations DHL Supply Chain and Diageo (KBL) East Africa’s joint customer workshop in East Africa focused on innovative solutions for warehouse and transport operations. This collaboration advanced key initiatives, including the IoT-Smart Sensor Value Proposition, Data Analytics Value Proposition, Applied Analytics, and bionic enhancements for safety. Leveraging Internet of Things (IoT) technologies, the IoT-Smart Sensor initiative provides real-time insights into the condition and location of goods. This innovation optimises inventory management, reduces transit times, and enhances operational efficiency, delivering exceptional value to customers. Bionic enhancements aim to improve safety in warehouse and transport environments through wearable technologies and augmented reality. These innovations elevate workplace safety standards, reduce accident risks, and enhance productivity. On-road safety is further enhanced by on-board smart cameras integrated into DHL’s Digital Control Tower. These cameras offer real-time visibility, accident prevention, evidence collection, driver behaviour monitoring, cargo security, compliance assistance, and cost savings. Applied Analytics, emphasised during the workshop, uses advanced models and algorithms to uncover patterns, trends, and correlations within complex datasets. This enables predictive maintenance, demand forecasting, and route optimisation, leading to operational efficiency and significant cost savings for Diageo, especially in managing truck turnaround times at customer plants and key distributors. The Data Analytics initiative, delivered through the digital connected transport solution, refines how data is harnessed to drive informed decision-making. Sophisticated analytics tools unlock actionable insights from vast data volumes, empowering clients to make strategic business decisions confidently. This transformation of data into actionable intelligence helps businesses in East Africa gain a competitive edge and adapt to dynamic market conditions. DHL continuously pushes industry boundaries. These initiatives have a transformative impact on logistics, and DHL seeks industry recognition for its commitment to innovation and change management.
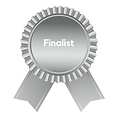

DHL Supply Chain South Africa – WMOS implementation
Transition to Excellence: The Implementation of WMOS at DHL Supply Chain In May 2022, DHL Supply Chain South Africa began systematic operations on the Warehouse Management Operating System (WMOS), while concurrently transitioning from a competitor’s logistics system (Stockkeeper). To maintain control over inventory management, stock rotation, and batch controls, we implemented robust Standard Operating Procedures (SOPs) and Work Instructions. The WMOS implementation was a transformative move, offering enhanced system features and capabilities to manage both Outbound and Inbound stock transfer orders. Along with daily automated reports, it propelled DHL forward, providing the client with transparent daily visibility into inventory management. This reassured the client that their inventory was managed by cutting-edge technology, namely the WMOS, and instilled a sense of comfort. Despite the challenges, DHL managed to transition this project in record time, taking over from the previous logistics provider as the primary 3PL supplier without causing any disruption to the business operations. By the end of 2022, the transition period ended with a loss of R500k. However, in 2023, stringent processes were put in place for accountability for each case. Regular updates with the Inventory team helped in reconciling the previous weeks tasks and planning for the current week. The annual 2023 stock count ended with a positive result. This transition showcased how DHL Supply Chain Africa effectively managed the changeover from the previous logistics provider and significantly improved the state of our Outbound hard stand and GRA cage areas.
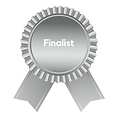

Kaizen Institute
The power of 5S The 5S methodology aims to improve efficiency, safety, and quality in the workplace by creating a clean, organised, and standardised environment. It is widely used in various industries beyond manufacturing, including healthcare, offices, and service sectors, to enhance productivity and reduce waste. During the implementation of a 5S Kaizen project at an outdoor engineering laydown area in a South African Mining Processing site, the Kaizen Institute uncovered a significant challenge: several engineering workshops were overflowing with poorly stored inventory, both in “squirrel stores” and the main store. Upon investigation, they pinpointed the root cause—a lack of trust in the on-site supply chain team and stores to provide the necessary resources promptly. Facing budget constraints, the 5S team took decisive action. They utilised the principles of 5S to establish robust inventory control systems within their domain. This initiative not only addressed current concerns but also facilitated the return of stock items to central stores. Moreover, it led to the identification of surplus items worth R3.4 million, earmarked for auction. This strategic approach not only streamlined operations but also yielded substantial financial benefits, marking a pivotal achievement in enhancing efficiency and resource management at the site.
Transport (all modes & intermodal)
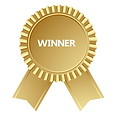

DHL Supply Chain South Africa – Euro 5 Fleet
Taking the next step to a cleaner, greener future As part of the drive to reduce logistics-related greenhouse gas (GHG) emissions, DHL Supply Chain South Africa has embarked on a journey to reduce its carbon footprint by investing over 7.3Mil Euro in a new fleet of Euro 5 Trucks in South Africa. This in turn will make the new Fleet one of the largest Euro 5 fleets in the country. DHL Supply Chain has invested over 300k Euro to replace the entire fleet in Uganda and is the first cluster to measure carbon emissions by Truck and Driver, even down to forklifts. These investments demonstrate the commitment to running a more sustainable fleet and taking the next step to a cleaner, greener future. Previous challenges faced with the existing (outdated) fleet included severe downtime, excessive maintenance costs and decreasing service levels to our customers. By embarking on this journey, DHL aims to reduce and possibly eliminate some of these challenges. In addition, 29% less CO2 and 60% less NOx emissions will be released into the environment. The goal is to position DHL as the market leader in sustainable transport by investing in more sustainable solutions across Africa. With competitive maintenance quotes, extended service intervals, and better performing fuel consumption, DHL will be able to provide the market with a cleaner more efficient solution, all at the same cost. In addition, DHL is in the process of initiating a BEV trail which will play an important role in contributing to the DHL Group target of <29mn tonnes of carbon emissions by 2030, as well as moving to the mission of Zero Emissions by 2050.
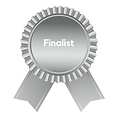

Petit Forrestier
Leading the Way in Refrigeration Fleet Rental Founded in 1907, Petit Forestier is a family-owned business and the European leader in refrigeration fleet rental. Petit Forestier boasts 80,000 vehicles, 300 branches, a 2023 turnover of 1,080 million euros, and over 15,000 clients. In 2018, Petit Forestier expanded to South Africa, establishing branches in Johannesburg, Durban, and Cape Town, with a fleet of over 350 vehicles nationwide. The company’s mission is to ensure the operational continuity of the cold chain with a wide range of refrigeration products and high-quality, personalised services, 100% focused on refrigeration. What makes Petit Forestier unique is its status as a one-stop shop, with trained technicians capable of working on a wide variety of problems. This ensures that clients receive comprehensive and efficient service, minimizing downtime and maximizing productivity. Petit Forestier is also the only rental company in South Africa offering a unique Buy Back service. This allows Petit Forestier to purchase a client’s fleet at current value, enabling clients to reinvest in their business. Petit Forestier then takes over the fleet’s maintenance and upkeep responsibilities. A major success of the Buy Back offer occurred in 2022 with the purchase of Henties’ fleet. Founded in 1998, Henties is a household name and market leader in South Africa. With funds from the fleet sale and their resources, Henties purchased a farm with the oldest and largest water rights, securing their growth in the South African market. The Buy Back service allows clients to focus on their core business while Petit Forestier handles fleet management. This service includes decisions on truck replacements, cost savings on maintenance, and freedom from concerns about tires, licenses, or breakdowns. This flexibility and assurance help clients meet demand and enhance production. By focusing on what they do best - fleet management - Petit Forestier enables clients to invest more in their product and business growth, resulting in a massively positive impact.
Technology Information Systems


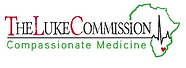
The Luke Commission powered by Luvelo
People-centred digital eco-systems The Luvelo Enterprise Suite, developed by Luvelo Solutions LLC and piloted by The Luke Commission (TLC) in Eswatini, manages supply chain logistics through interoperable apps. Pronounced “lue-vell-oh,” derived from the Siswati word for compassion, Luvelo enhances service delivery through accountability, transparency, and operational excellence. TLC needed a robust digital platform to deliver comprehensive healthcare to over 300,000 patients annually. Existing solutions were inadequate, prompting TLC to develop Luvelo, a scalable, mobile-first platform that streamlines supply chain networks and integrates with other organizational systems. Built on the low-code Outsystems platform, Luvelo incorporates insights from practitioners to address supply chain challenges in resource-limited contexts. The system features facial recognition, digital signatures, and photo documentation, ensuring accountability and transparency even in low-bandwidth environments. Luvelo provides end-to-end supply chain accountability from purchase to distribution, minimizing warehouse and pharmaceutical shrinkage. Transactions can be initiated offline, ensuring continuity regardless of network availability. Features like barcode scanning and Bluetooth integration with label printers simplify inventory management, enhancing operational efficiency. The platform also includes apps for fleet management, task management, help ticketing support, work orders, and product distribution. Luvelo’s integrated platform eliminates the complexities of disparate systems, optimizing resources and saving time and money. In healthcare and other settings, this system saves lives through accountable and transparent supply chain management. The pilot at TLC manages over 18,000 unique items and has completed over 2.3 million inventory operations, serving more than 700,000 patients. Following a successful pilot, Luvelo has scaled to accommodate millions of simultaneous users and is now available for licensing worldwide, empowering even small organizations to deploy national-level solutions.
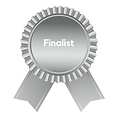
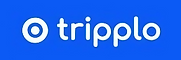
Tripplo
Logistics Software
Shaping the Future of Logistics Management Tripplo, a leading logistics software company, is dedicated to being the best end-to-end logistics platform globally. With a vision set on excellence, Tripplo has achieved remarkable milestones: 7,000 monthly loads, 6,000 active fleets, a gross monthly merchandise value of R3 billion, and a monthly transactional value of R100 million. Tripplo offers valuable tools and services for transporters, optimising operations and maximizing efficiency. The rates engine allows transporters to manage rates, access historical data, and gain insights into lanes, routes, and truck types. For cargo owners, Tripplo provides comprehensive solutions to streamline logistics and enhance visibility. The loads engine automates load management from order to payment, ensuring efficient allocation and seamless matching with transporters. Real-time tracking through the loads tracking feature allows cargo owners to monitor cargo status and transporter locations, ensuring timely delivery and peace of mind. Tripplo’s commitment to technological advancements extends beyond just providing a software solution. From revolutionising document storage with secure, centralized repositories to enhancing load tracking with real-time updates. Tripplo has demonstrated excellence in leveraging technology for supply chain innovation, delivering tangible value for both transporters and cargo owners and has demonstrated mastery in adopting cuttingedge technologies and delivering transformative solutions.
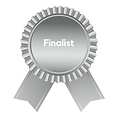

Mondelez South Africa
In 2022, Mondelez South Africa appointed the first Digitization Lead for Customer Service and Logistics. During this period, they led the automation of a daily business dashboard that indicated business performance. The report, now published twice a day instead of once, takes less than 45 minutes to generate compared to the previous 3 hours, resulting in a significant resource saving. This automation enabled accurate and quick business decision-making, cross-functional transparency and collaboration, and improved operational efficiency. They also implemented a vendor management Inventory tool, adopted from Mondelez EU, within the South African distributor. Leading this project with the local and regional team, they managed distributor inventory through Mondelez and automated order recommendations. This resulted in a 90% reduction in expired products, an increase in service levels from 70% to 88%, an impressive headcount reduction, a shortened delivery lead time to customers of 72 hours, and greater information transparency within the distributor through system-generated reporting. Due to these innovations, the department became more customer-centric, as reflected in the Advantage Survey (AGI), where Mondelez was rated in the top 10 from number 26. In 2023, they were rated in the top 5.
Supply Chain Co-ordination and Collaboration


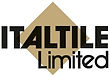
Inhance
Supply Chain Solutions and Italtile
Limited
A Blueprint for Collaborative Excellence In South Africa’s evolving home improvement sector, Italtile Limited stands out for innovation, efficiency, and sustainability. This entry for the Supply Chain Co-ordination and Collaboration category highlights the transformative partnership between Italtile Limited and Inhance Supply Chain Solutions, which began in 2017. Founded in 1969, Italtile Group is a leader in manufacturing, franchising, and retailing tiles, bathroom ware, and home-finishing products, supported by a vertically integrated supply chain. The collaboration with Inhance aimed to revolutionize Italtile’s distribution operations across its manufacturing, distribution, and retail businesses. Inhance initiated a holistic approach to dismantling decentralized planning silos, leveraging innovative technology and strategies for integrated network planning and enhanced visibility. Working closely with Italtile’s IT and Operations teams, Inhance designed and implemented a flexible, scalable solution tailored to the group’s diverse needs. This shared vision focused on building integrated solutions that could grow with the business. The collaboration resulted in an integrated Supply Chain Control Tower Solution, seamlessly fitting into Italtile’s operations. This fully outsourced 4PL solution included a dedicated planning operations team and scalable products like TMS Control Tower, Transportation and Load Optimization Solvers, and Yard Management Solutions. These components supported Italtile’s vertically integrated supply chain, enhancing sustainability and efficiency across manufacturing, distribution, and last-mile delivery. The Italtile-Inhance collaboration exemplifies supply chain co-ordination and collaboration, driving operational efficiency, cost-effectiveness, and environmental sustainability.
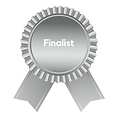

Right
ePharmacy
Revolutionizing Healthcare Access in Lesotho Efficient supply chain management is crucial for equitable healthcare access in Africa, yet many regions face logistical hurdles and fragmented systems. Right ePharmacy’s innovative BonoloMeds™ programme in Lesotho exemplifies a transformative approach to decentralized drug distribution and collection, enhancing healthcare outcomes through patient-centric solutions. In Lesotho, supported by USAID funding and in collaboration with Right to Care and the Ministry of Health, BonoloMeds™ addresses chronic patient burdens by introducing a 4-in-1 programme. It features a Central Dispensing Unit (CDU), Prescription scanning for data digitization, a logistics App, and Collect&Go™ smart lockers. These innovations significantly reduce clinic visits, enhance patient convenience, and optimize supply chain processes. Collect&Go™ smart lockers serve as efficient alternative pick-up points, empowering patients to conveniently collect medications. This patient-centred approach improves medication access and management, relieving pressure on healthcare facilities. BonoloMeds™ leverages warehouse management systems and electronic record systems for real-time data on stock levels and demand. This data-driven approach optimizes inventory management, identifies bottlenecks, and facilitates informed decisionmaking, enhancing overall efficiency. The programme has successfully enrolled thousands of patients, demonstrating its scalability and adaptability across diverse healthcare settings. It has streamlined logistics, improved healthcare access, and empowered local workforce through continuous training and support. Right ePharmacy remains committed to advancing healthcare through innovation, collaboration, and data-driven solutions, ensuring sustainable improvements in healthcare access and patient outcomes.
Innovation & Change Management



Inhance
Supply Chain Solutions and Twinsaver Group
Transformative supply chain practices Initially facing substantial operational challenges that threatened its market position, Twinsaver Group embarked on a strategic overhaul focusing on people and technological investments, catalysed by Inhance’s expertise. Central to the project’s success were several key elements. Twinsaver integrated a Linear Programming engine for factory planning and adopted advanced technology solutions such as a Warehouse Management System (WMS), Transport Management System (TMS), and a Supply Chain Control Tower. These innovations optimized production scheduling, streamlined logistics, and provided real-time visibility, enhancing decision-making and operational efficiency. In a bold move, Twinsaver outsourced its logistics operations to Inhance in a comprehensive 4PL capacity. This included managing warehousing, primary and secondary transport, courier services, and call centre operations. The transition involved a rapid deployment of resources and specialists, achieving sustainable operations, cost savings, and improved service levels within a tight timeframe. Effective change management strategies, including online platforms and on-site training, facilitated a seamless adoption of new systems and processes across Twinsaver’s workforce. This approach fostered integration and communication, crucial for achieving collaborative success and operational alignment. The project delivered significant financial and operational improvements, evidenced by a notable increase in EBITDA and substantial reductions in inventory holding costs and logistics expenses. Logistics costs as a percentage of sales decreased significantly, underscoring the project’s impact on bottomline performance and operational efficiency. Moreover, the initiative strengthened vendor and customer relationships, promoting a more responsive and agile supply chain that supports Twinsaver’s leadership aspirations.
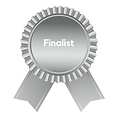

Takealot
Why be average when you can be great? This ethos resonates with South Africa’s history of pushing boundaries, such as achieving the first heart transplant. The challenge was set to become the first e-commerce retailer certified in more than three ISO systems, transcending mere compliance to achieve groundbreaking standards. With steadfast determination and strong support, this journey began with a target of achieving full certification by 2028. Thanks to unwavering commitment and collaborative effort across all levels, this timeline was accelerated, culminating in November 2023 when auditors meticulously reviewed the entire Integrated Business Management System (IBMS) over ten intensive days. The culmination of this effort came during the closing meeting, where the auditors recommended TAL for certification across all ISO systems as per the defined objectives and audit outcomes. This achievement marked a historic milestone as Takealot (TAL) became the first to implement an Integrated ISO management system of its kind, uniquely combining six different ISO standards into a cohesive whole. This innovative system, developed internally due to its unprecedented nature, integrates multiple-tier standards across departments, fostering harmony and coherence while enhancing critical thinking. Its success hinged on a deep technical understanding of each department’s requirements and how they align with ISO standards. Such integration was only feasible through wholehearted buy-in from all management levels, aligning departmental goals toward a unified objective. Methodologically grounded in ISO 9001, 14001, 22000, 26000, 31000, and 45001 standards, this approach not only adapts to a dynamic business environment but also ensures alignment with other management systems, emphasizing continuous improvement and risk mitigation. This achievement underscores TAL’s pioneering spirit and commitment to excellence in organizational management and standards compliance.
Training & Talent Management
Innovation & Change Management



Girls on the Move
Addressing gender disparity and skills shortages The Girls on the Move (GotM) initiative, launched by Pamela Steele Associates (PSA) in July 2022 in Kisumu, Kenya, addresses the gender disparity and skill shortages in health supply chain roles across Africa. Traditionally overlooked, supply chain management lacks specialized skills, particularly among women who constitute only 27% of management positions despite comprising 43% of the workforce. Coupled with high youth unemployment rates averaging over 20%, and sometimes peaking at 70-80% in some regions, women face disproportionate challenges. Sponsored by the Reproductive Health Supplies Coalition (RHSC), GotM initially piloted with 30 young female graduates in Kisumu, later expanding to include 6 additional interns in Nairobi. The programme provided 8 months of practical experience in various supply chain roles. Notably, 21 interns secured permanent positions in esteemed organizations such as Mission for Essential Drugs and Supplies, USAID Dreams Project, and Kenya Revenue Authority, among others. Testimonials from graduates like Mercy Odhiambo and Margret Omondi highlight the programme’s impact on career development and skill acquisition. Mercy gained extensive knowledge in health supply chain practices and now applies her skills in the hospitality sector. Margret, having pioneered a procurement manual, pursued further education in humanitarian logistics and supports her family financially. PSA plans to scale GotM in collaboration with partners, aiming to train and graduate 500 interns across multiple counties in Kenya and expand into another country within five years. The initiative’s goals include bridging the health supply chain skills gap, enhancing women’s professional growth, and establishing sustainable career paths for programme graduates.

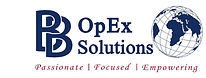
Bridge Building
OpEx
Solutions
Uplifting Women in Africa While Helping to Close Supply Chain Talent Gap In collaboration with the Association for Supply Chain Management (ASCM) Foundation and the U.S. President’s Emergency Plan for AIDS Relief (PEPFAR), BBOpEx implemented an initiative to provide young women in South Africa with the necessary skills to compete for high-quality, good-paying jobs in the supply chain industry. The program aimed to empower Adolescent Women & Young Girls (AWYG) in sub-Saharan Africa, who are disproportionately affected by the HIV/ AIDS epidemic, by providing them with training in Essential Supply Chain Management skills. The program was designed to help these young women access employment opportunities and achieve economic independence, which is a key factor in supporting them to stay HIV-free. The program commenced in South Africa where 100 young women between the ages of 18-24 were trained to be the next generation of supply chain professionals in the region. The impact of the program on participants was profound and far-reaching. Although not all the participants secured immediate employment, the skills and recognition earned were invaluable assets that will distinguish them as they progress in their careers. Participants who secured employment became role models within their communities, inspiring other young women to pursue education and career opportunities. This created a ripple effect of empowerment and aspiration within the community.
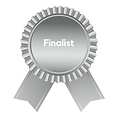
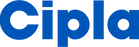
Cipla South Africa – Fostering Talent and Inclusion
Fostering Talent and Inclusion Established in 1935, Cipla is a global pharmaceutical leader focused on sustainable growth and expanding its portfolio in key markets like India, South Africa, North America, and other regulated and emerging markets. Known for its strengths in respiratory, anti-retroviral, urology, cardiology, anti-infective, and CNS segments, Cipla South Africa stands as the third largest pharmaceutical company in the country, excelling in both private and tender markets. The Roleto- Role initiative fosters talent development by encouraging employees to take on a second role in another department for a year. This programme, marked by rigorous selection, has not only reduced recruitment costs but also boosted employee morale and enhanced workforce skills. Notably, R2R has enabled employees to excel in roles they might not have traditionally pursued, strengthening Cipla’s organizational culture. Recognising South Africa’s diverse history and educational challenges, Cipla initiated the Recognition of Prior Learning programme. This initiative targets employees without formal qualifications, providing them with literacy and communication skills. Through RPL, ten employees successfully completed the programme with a 100% pass rate, gaining formal qualifications that align with their knowledge and skills. This programme not only enhances employability but also promotes lifelong learning, social inclusion, and selfesteem among participants. Cipla South Africa’s progressive approach to talent development and inclusivity underscores its commitment to fostering a workplace where every employee feels valued and empowered to reach their full potential. These initiatives not only benefit individuals but also contribute to Cipla’s overall success and leadership in the pharmaceutical sector.
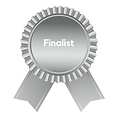
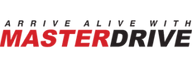
MasterDrive
The importance of Advanced Training Solutions MasterDrive, a leading provider of advanced driver training solutions in South Africa offers practical rollover prevention training. This pioneering approach aims to enhance road safety and mitigate financial losses within the transport sector. Prior to the development of the MasterTrucker Rollover Prevention Training Programme, South Africa grappled with significant safety challenges in road freight transport. The transition from rail to road transport resulted in a rise in fatal truck accidents many caused by rollovers. In 2010, Afrox encountered 11 rollovers in its tanker fleet, each incident causing approximately 1 million Euros in losses and posing grave safety risks. Seeking a solution, Afrox turned to MasterDrive for assistance. Recognising the gravity of the situation, MasterDrive conducted a thorough analysis of the root causes of these rollover incidents, emphasizing a uniquely African perspective. The findings underscored the urgent need for comprehensive, practical training tailored to the specific challenges faced by truck drivers, particularly in the liquid and dry bulk industries across the African continent. In collaboration with Afrox Linde Group, MasterDrive launched the customdesigned MasterTrucker Rollover Prevention Training Programme in 2012. This innovative initiative introduced custom-designed rigs equipped with outriggers, enabling practical, realtime training in a controlled environment. The programme’s advanced capabilities include real-time monitoring facilitated by specialized Wi-Fi cameras, allowing drivers, passengers, and remote supervisors to observe training during rollover simulations. Further enhancing safety, the programme incorporates a robust military-spec 5th wheel design to bolster vehicle stability and withstand forces during rollover incidents. MasterDrive is actively advocating for legislation mandating rollover prevention training for all truck drivers. Continual updates to training methods and tools integrate the latest safety technologies and practices, fostering global partnerships to promote road safety and align with UN Sustainable Development Goal 3.
Preservation of the Environment
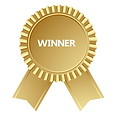

DHL Supply Chain South Africa – Saving Africa’s Vultures
Saving Africa’s Vultures Usually when you see vultures moving around in South Africa, they’re flying. Earlier this year, DHL embarked on a remarkable journey in partnership with non-profit vulture rehabilitation group Vulpro to transport 160 Cape and African White-backed vultures, notoriously sensitive birds, from a Vulpro reserve in Hartbeespoort, near Pretoria, South Africa, to Vulpro’s Shamwari Game Reserve, Gqeberha (formerly known as Port Elizabeth) in the Eastern Cape. This was the largest move of its kind in Africa – an unprecedented logistical challenge. This 16-month project involved 50 people to coordinate and the total distance driven was 1,042 kilometres (around 650 miles) in an overland journey which took 18 hours. This is the fourth release that DHL has successfully executed with Vulpro and so far the results look promising, as more sightings of Cape Vultures are being recorded. DHL handled all the logistics and security, while WeWild Africa, an NGO specialising in animal rewilding and translocation, loaded the birds and funded the 160 transport crates. In addition, DSC joined forces with Born Free for a second trip down to Shamwari, where Tsar and Jamil, two lion brothers who were rescued in Ukraine, were transported back to their ancestral land. The two brothers travelled a whopping 8,000 miles to South Africa where DHL Supply Chain collected them from OR Tambo Airport and drove them down to Shamwari, ensuring every step of the young brothers’ journey was smooth and safe. The total distance driven was over 1000 kms.
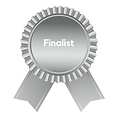
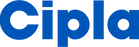
Cipla South Africa
Environmental Stewardship The Cipla Distribution Gateway in South Africa exemplifies Cipla’s commitment to environmental stewardship through several groundbreaking initiatives. Cipla installed 1,088 specialized solar PV panels covering 16,000 square meters of roofing, integrating a 450kVA inverter system with the site’s generators. This initiative significantly reduces diesel consumption during load shedding, curbing energy usage and emissions. On 1st November 2023 Cipla implemented a waste to landfill initiative which sorts recyclable materials such as cardboard, paper, and plastics onsite. Kitchen waste is also segregated and processed offsite, maximizing recyclable recovery and minimizing landfill contributions. Aiming to foster a culture of sustainability, Cipla’s facility hosts a reverse vending machine in partnership with Imagined Earth. Employees compete to recycle barcoded glass and plastic bottles from both workplace and home environments, promoting environmental consciousness and participation. Environmental data at Cipla Distribution Gateway is meticulously tracked and shared monthly, ensuring transparency and accountability. These initiatives not only benefit the business operations but also contribute to a healthier environment and community engagement. Cipla’s dedication to sustainable practices and innovative solutions underscores the commitment to creating a better future for generations to come, setting a benchmark for corporate responsibility in the pharmaceutical industry.
Training & Talent Management
Unique Supply Chain Projects
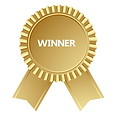
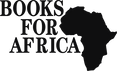
Books for Africa
Books for Africa’s primary mission is to end the book famine in Africa by collecting, sorting, and shipping books to countries across the continent. Their goal is to promote literacy and education by providing access to books and educational materials. The organisation stands out for its commitment to improving education and literacy in Africa through the simple yet powerful act of providing books, thereby empowering generations with knowledge and opportunities. Books for Africa is the largest shipper of donated text and library books to the African continent shipping over 60 million books to all 54 countries on the African Continent since 1988. In 2023 alone Books for Africa shipped approximately 4million books valued at over US$32million to 32 different African countries. Books for Africa is proud of its strong financial health and ongoing accountability and transparency and proud to have been designated as a “Give with confidence” charity. The organisation operates with a lean structure, ensuring that the majority of donations go directly to their mission of shipping books. They leverage volunteers and partnerships to maximize their impact and reach Books for Africa partners with many organisations including the African Union NGOs, Ministries of Education, US Embassies and universities across Africa as well as donor, publishers and other partners. A true example of supply chain collaboration. Books for Africa believes that education is the greatest equaliser in the world providing opportunity for poor and disadvantaged to rise above their circumstances. The organization has had a profound impact on education and literacy rates in African countries.
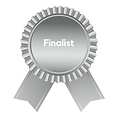
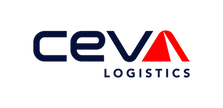
CEVA Logistics
In the remote region of Tanzania, the construction of the Julius Nyerere Hydropower Plant and Dam, one of Africa’s largest hydroelectric projects, nears completion. CEVA Logistics has undertaken the formidable task of managing logistics for this project, which involves transporting over 55 large transformers, among the world’s largest ever produced, through challenging terrain. The project’s location presents significant logistical hurdles, exacerbated by the size and sensitivity of the cargo. Each transformer, comparable in dimensions to seven saloon cars, must traverse rugged African roads to reach the site safely. These transformers, critical to the project’s infrastructure, have a procurement lead time of at least ten months, underscoring the importance of careful handling to prevent delays or damage. CEVA Logistics employs meticulous planning well in advance of cargo departure from the Port of Dar es Salaam. This includes assessing soil bearing capacity, ensuring sufficient handling equipment availability at transit points like rail stations, and mitigating the impact of environmental factors like wind. Moreover, the project involves complex multi-modal transportation, spanning road, rail, and specialized trailer journeys, each stage meticulously orchestrated to minimize risk and ensure cargo integrity. For instance, transporting the 111-ton, 8-meter long Rotor Body for the Francis Turbine required over six months of planning and involved coordination across 100 kilometres of road, 120 kilometres of rail, and 40 kilometres of gravel to the project site. Despite these challenges, CEVA Logistics has successfully delivered over 85% of the out-of-gauge cargo to the site. This unprecedented engineering feat in East Africa underscores their commitment to pioneering logistics solutions for large-scale infrastructure projects.
International Business
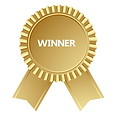

Futuretend
A small company taking on big challenges Futuretend successfully negotiated and partnered with two companies as financial partners, enabling the facilitation of multimillion-rand transactions exporting sugar and frozen chicken from Brazil predominantly to China and Africa. The process was made possible by using specialist knowledge of the medical sector with SAHPRA when applying for General Administration of Customs of China (GACC) registration which enables Futuretend to be pre-approved as an exporter. Similar registration processes of supply sources in Brazil were also required. The GACC system requires stridulent rules and regulations that needs to be adhered to, to be able to have a successful export and import transaction. The second hurdle was to find a financier who was willing to back the financial instruments to protect the supply sources for one and secondly to facilitate “nontransferable” payment instruments for instance MT700 letter of credit. The last hurdle was to appoint a Chinese representative in China to overcome the language and cultural barrier. After plenty of research this is one of the most important factors to have in place for successful transactions. After addressing all these hurdles and challenges Futuretend streamlined a process where they successfully transact, from engaging with foreign buyers in their own language, accepting their payment instruments and fully fund it with the finance partners to pay the suppliers and export the goods from another foreign country to another foreign country. This entire process took a year to get to execution stage. Throughout the process it was necessary to learn about new products, new regulations, new ways of doing business. Being a small company taking on big challenges
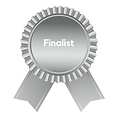
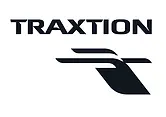
Traxtion
A pivotal force in Africa’s evolving rail sector Construction on Africa’s first railway line commenced in Egypt in 1852, marking the continent’s debut into efficient transportation for people and freight across vast distances, bolstering regional and international trade. Today, 172 years later, African railways maintain their pivotal role, poised for greater impact with supportive investment policies. Traxtion, a key player boasting one of Africa’s largest private freight rolling stock fleets in its 36-year history, facilitates essential connections across the continent. By enabling the export of mineral wealth, Traxtion generates revenue for governments and mining firms. For instance, it moves 1.5 million tons of freight annually between Ndola and Dar es Salaam, supporting trade in copper from the DRC and coal from Mozambique. Traxtion’s locomotives transport fuel and containerized goods in Zimbabwe and provide traction across Zambia, Senegal, Tanzania, and Angola. Operating across borders poses challenges, but Traxtion leverages its expertise and partnerships to navigate these complexities effectively. Tailoring rail solutions to African conditions has cemented Traxtion’s leadership in sub-Saharan freight rail. In South Africa, Traxtion supports mining by transporting minerals to refineries and export facilities. With impending rail reforms, it anticipates expanding as a third-party operator, stimulating the economy and job creation. Positioned to capitalise on opportunities under the African Continental Free Trade Agreement (AfCFTA), Traxtion enhances regional trade gateways and fosters economic growth.