




2023 WINNERS
View the Photos from the 2023 Awards Dinner
The Africa Supply Chain Excellence Awards recognise the vital role played by the supply chain management profession, and honour and celebrate the outstanding achievements of organisations and individuals working in the field in Africa.
The Directors report an overwhelming response to the awards this year, with 92 entries received from 26 countries around Africa. Launched in 2022 as a collaboration between leading industry organisations, the awards enable industry cooperation and knowledge sharing, in addition to promoting excellence in supply chain management. They also aim to drive awareness of the growing imperative to “green” supply chains and ensure that all supply chain components – from sourcing and procurement to distribution – are genuinely sustainable and environmentally responsible.
2023 Sponsors
JUDGES AWARD FOR EXCELLENCE

NCT FORESTRY AGRICULTURAL CO-OPERATIVE LIMITED
NCT Vryheid Road to Rail Logistics entered into lengthy negotiation with Transnet and was able to open the NCT Road-to-Rail transhipping and procurement depot facility on 4 November 2019 within the Vryheid East marshalling Yard. Prices are derived from Richards Bay mill delivered prices less the railage, handling and on-site capital & running expenditure for the weighbridge, solar, fencing and staffing. Suppliers in the catchment save from R40/ton to R70/ton, compared with the road to R/Bay option, which means NCT’s capital spend of R4,7million was recovered in ±9 months with ongoing annual savings of ±R5,3million. NCT installed an 80-ton weighbridge, duly permitted by the KZN Department of Transport which allows NCT to accept PBS vehicles. A Kobelco SK210 excavator with a Matriarch MT 800 grab does the timber handling. Delivery specifications, stock management and truck scheduling systems are the same as at chip mills in R/Bay. Going Green! Solar panels and gel batteries ensure the weighbridge, lighting and electric fence operates independently from ESKOM. At 80 000tpa throughput, NCT removed 2350 trips per annum between Vryheid and R/Bay with obvious externality benefits to road safety and congestion. With timber trucks consuming ±60l/100km this save 1 500g CO2/km or 1 552 tons CO2 emissions per year! The long run cost creep on rail is also less than road as rail only use 8% diesel in setting tariffs while road assumes ±40%.
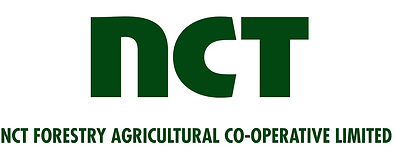
EXCELLENCE IN SUPPLY CHAIN EDUCATION & YOUTH PROGRAMMES

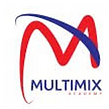
Multimix Academy Nigeria
MULTIMIX, NIGERIA. Multimix Academy is Nigeria's award-winning multifaceted company with specialization in Global Trade, Logistics and Supply Chain Management with over 20 years of consistent value creation and industry leadership. Since 1997, Multimix Academy has remained committed to providing tailored learning experiences, professional certifications, training and capacity-building initiatives for mid/senior-level workers and executives across Nigeria’s supply chain management and logistics industries. We have also provided knowledge support and leadership development programs for industry stakeholders in the last decade. There are academies, and there is us, differentiated by our excellence in service delivery, inclusive learning methodologies and customer-focused solutions designed to enhance professional development and organizational efficiency.

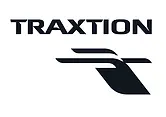
Traxtion Training Centre
TRAXTION experienced a shortage of relevant skillsets to service its business that the market also could not respond to. As a major player in the industry offering rail operations and technical qualifications, Traxtion is keenly aware of the consequences of not being able to retain or transfer knowledge and expertise and this fueled its determination to address the supply of scarce skills in the rail sub-sector. Traxtion is registered as a Skills Development Provider for rail operations and technical qualifications, for our staff and key markets on the African continent. The Traxtion training Centre is accredited by the Transport Education Training Authority (TETA) as well as the Quality Council for Trade and Occupations (QCTO). To date more than 700 drives and 75 red seal technicians have been trained. Traxtion offers 25 rail-related courses; qualifications range from NQ Level 3 – 5; it conducts an average of 700 training interventions annually; has a training footprint in at least eight African countries, and has trained its own and 16 third parties on various rail novice and refresher interventions. All of this is done to build a pipeline of skilled and competent individuals who can make meaningful strides towards increasing the supply chain competitiveness of our industry.
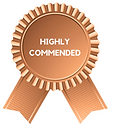
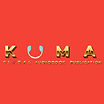

Kuma & Promike Audio Books
KUMA AND PROMIKE AUDIO BOOKS is a company that converts written publications: educational, fiction, non-fiction into indigenous languages. It works with self-published authors and publishers who pay for the conversion. The Audiobooks are currently distributed by thumb drives with the intention in the future to create an app for people to be able to use. This initiative is very helpful for school children who can't read and write, and university students who are not coping with reading lengthy study materials. It is also helpful to people who can't find time to read as they can play the Audio Books on their mobile phones.
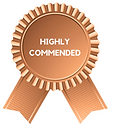

EY Supply Chain Services
The EY Supply Chain Services (SCS) team launched the initiative "SCS Stepping Up for the Children" in aid of Mother of Peace, a non-profit orphanage and safe house in South Africa. The program, launched in August 2022, consisted of two principal components; 1. A fitness challenge, in which individuals or teams of participants across EY SCS "sponsored" one or more students through steps walked, kilometres run, minutes of exercise, etc., which were tracked and subsequently translated into funds donated to the children’s educational costs. 2. A Zoom-based mentorship programme that paired selected EY SCS volunteers with a mentee from Mother of Peace to help them develop the knowledge and skills necessary to prepare for their entry into the working world. The programmes outcomes were as follows: 97 participants across EY SCS 27 children at Mother of Peace received mentoring | 67 students benefited from donations towards school supplies, uniforms, and other expenses | Two children received financial support for legal paperwork rectification | 80 gift vouchers were given to the children during the holiday season. Phase 2 of the initiative has been scoped, with plans to introduce internships, bursaries, and small business incubators.
INNOVATIVE SUPPLY CHAIN PROJECTS AND OPERATIONS


CEVA Logistics
One third of Niger’s 18 million population is facing food insecurities; they heavily depend on consistent aid & relief supply. However, the logistics of getting food from Togo’s Lome port to this landlocked county is a challenging task. The situation was significantly exacerbated due to the continued Jihadists attack in Burkina Faso red zone as the standard route from Lome to Niger’s Niamey passes through the red zone. In 2022, when CEVA Logistics was awarded its first commission by a high-profile international aid agency, the attacks were at their peak. Although many other logistics services providers either took a reckless risk (and many got their cargo and drivers detained) or simply backed off, CEVA Logistics embarked on a mission to make a historic change. CEVA Logistics worked tirelessly to analyse a new route, closely collaborate with the customs of Togo and Benin and push through a complex customs reform that established a new customs process and customs code at the check points that overrides Africa Third Country Law. This was not a simple re-routing of cargo where one route is taken as opposed to another route. Ever since the new route was established others now use it on regular basis.


Imperial, a DP World Company & Pick n Pay
PICK ‘N PAY AND IMPERIAL, A DP WORLD COMPANY have cultivated a successful partnership over the past 11 years. Initially providing transport planning and continuous improvement services, Imperial's offerings later expanded to encompass transport finances and service provider management, delivering significant savings to Pick n Pay. Pick n Pay relies on a complex system of external partners, internal functions, stores and outsourced entities. Coordination and collaboration are essential to ensure smooth functioning, and a legacy of transport agreements has made it difficult to optimise the supply chain from both a service delivery and cost perspective. As part of an RFP process, Imperial presented a transformative proposal to unlock improvements in logistics and store operations. The work was awarded to Imperial in 2022. These improvements include the implementation of Imperial as outbound transport service provider in the inland region, inclusion of a variable fleet to optimise market flows, operational initiatives to address historic labour and logistics cost premiums, enhanced control and optimisation of inbound spend to drive savings. The result is an unprecedented example of Imperial showcasing multiple capabilities within a single solution delivering an integrated end-to-end logistics control tower, laying the foundation of end-to-end supply chain coordination and leveraging of synergies across multiple networks.
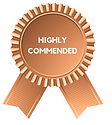

IMCD South Africa and Santova Logistics
IMCD is a global leader in the distribution and formulation of specialty chemicals and ingredients, providing solutions to its customers and partners. IMCD’s supply chain strategy aims to ensure that each step in the supply chain can be executed in the most sustainable, compliant, and cost-effective way. With a significant network covering over 98 trade lanes across the world, the business has undertaken a significant business transformation of its international logistics. Partnering with Santova Logistics (a global provider of international trade and logistics solutions), a project was initiated to launch a centralised procurement and inbound logistics function. The aim is to target significant cost and service benefit to its customers and IMCD through an agile and dynamic supply chain. The centralisation of core administrative functions as well as improved logistics has reduced working capital expense requirements by over R4m through reduced lead-times and stock holding. In addition, IMCD’s partnership with Santova is targeting further cost and carbon benefits through optimised freight management and consolidating shipments at source to improve the tonne-km ratios. Although this journey is still in progress, IMCD has made significant strides in ensuring its supply chain can service its customers and business in a more cost and environmentally sustainable manner.


Imperial, a DP World Company - KAM Framework Project
IMPERIAL, A DP WORLD COMPANY, has a history of growth through acquisitions. This resulted in client overlap between business units, with clients often dealing with a number of Imperial representatives. Independent research also showed a low score for Imperial when it came to innovative ways to engage with clients. This led to the reengineering of our client management and engagement approach, resulting in the introduction of a Key Account Management (KAM) Framework. The KAM Framework included the development of structured communication plans and client segregation methodologies, as well as the formulation of comprehensive account plans. This was achieved through collaborative strategic internal sessions and streamlining integrated supply chain value propositions to clients based on their industry. The methodology behind the development of the KAM Framework was supported by research conducted by RAIN Group, which shows that using properly formulated account plans means that revenue is 3 times more likely to grow by 20% or more, and profit is 3.4 times more likely to grow by 20% or more, for strategic accounts. There is also 4.5 times more likelihood of significant client satisfaction improvement year-on-year.


Addendum and Tourvest Travel Services
In a pioneering move, Tourvest Travel Services (TTS) and Addendum Financial Technologies partnered to launch an innovative Supply Chain Finance (SCF) program that supported SA’s tourism industry, severely affected during the Covid-19 pandemic. TTS, a leading travel management company in South Africa, saw transactions plummet on the first day of Lockdown from around 11,000 a day to zero. The financial impact was even more devastating for the hundreds of SMMEs that comprise the bulk of the company’s supplier base. In response, TTS partnered with Addendum Financial Technologies to develop a solution that replaced Virtual Credit Card payments with SCF, eliminating transaction fees and thereby saving significant costs for suppliers. The change to SCF improved TTS’ gross margin by replacing costly, labour-intensive manual payment processes with automated solutions. This enabled the company to fund critical working capital during the pandemic and strengthen its industry leadership. The program resulted in an average cost saving for the 300+ suppliers (predicted growth is 5000 suppliers) that joined the program in the launch year. In line with ESG goals, Addendum and TTS' SCF programme is a zero-paper-waste solution. Based on the programme’s success, TTS plans to expand the program and is exploring how to bring customer bookings and payments into its SCF ecosystem.
ENVIRONMENTAL SUSTAINABILITY WITHIN SUPPLY CHAINS


Vector Logistics Pty Ltd - Solar Panel Van Project
Vector Logistics took significant steps towards environmental sustainability through partnering with experienced alternative energy companies. Initiatives implemented past 5-years: Water harvesting, recycling wastewater, diverting landfill food-waste, converting Lead Acid to Lithium-Ion MHE batteries, warehouse and vehicle Solar. Solar technology on refrigerated trucks reduces fossil fuel reliance, reduce carbon emissions and safeguard environment. 2-year 8-ton rigid trial at Peninsula depot with reputable suppliers, Mobius Energy Technologies and Thermo King. Trial results confirmed business case that 25% solar energy contribution and 75% Grid energy supply run fridge and tail lift continuously over 12 hrs. without using diesel. Saving 3.52 litres diesel per hour equates to average monthly CO2 reduction of 2.4 tons per vehicle. Vector implemented 4 additional solar units on 14-ton rigids. Solar benefits since Dec’22 for 5 rigids: R1 002 860 fuel savings, 89-tons CO2 reduction, reducing noise pollution and truck idling, 2.08 yr. ROI, 12-year life expectancy of solar equipment, vehicle type component interchangeability. Mobius portal track live Solar performance, enabling factual strategic investment decisions. Vector’s strategy towards Solar powered refrigeration demonstrates commitment to sustainable and responsible business practices. Resilient attitudes in Volatile, Uncertain, Complex, Ambiguous (VUCA) times, drives innovations to protect the environment and implement industry changing solutions.


DHL Global Forwarding
South Africa has hosted many global sporting and international racing events, but it has never hosted a FIA Formula E Event. A time sensitive project that required DHL Global Forwarding (DGF) to move around 120 Unit Load Devices totalling over 300,000 KG’s of cargo. Two Boeing 747-800’s and four Boeing 747-400’s aircrafts were utilized to complete the project coming in and out of Cape Town. Such a project required completion within 14 days from the previous week race in India to the following race after Cape Town in Brazil. The cargo that needed to be transported consisted of general goods, motor vehicles, racing cars and all the batteries (engines) for the Formula E cars. The batteries alone provided a unique challenge as this commodity requires special provision and exemption from the CAA authorities and it had to be completed within such short time frame. Cape Town International Airport is not a widebody freighter classified airport which created challenges with landing rights and permits, but it is also low on experience in handling such vast variety and sizeable commodities. Availability of sufficient equipment such as forklifts, trucks, and dollies to handle these loads within these limited time frames needed to be carefully planned. This enabled us to be able to process almost 200 import for re-export carnet clearances and still maintain compliance. The project was a complex process planned over 3 months from December 2022 to February 2023. DGF directly contributed to the success of the inaugural Formula E event in Cape Town which resulted in an estimated R2.13 billion in direct and indirect economic impact to the Western Cape in its first year alone.
RESPONSIBLE SOURCING AND PROCUREMENT AWARD


Reach Out Cameroon
REACH OUT CAMEROON is an NGO selected in 2020 as the Humanitarian Sub-Recipient (SR) to the New Financing Mechanism of The Global Fund to Fight AIDS, Tuberculosis, and Malaria. The grant is planned for 3yrs (January 2021 to December 2023). Community Health Workers are main actors for community Direct Interventions (CDI) providing basic health care to the local population in hard to reach areas. The North West and South West Regions of Cameroon have been hard hit by the ongoing political crises since 2016 to today and as a result the country is experiencing a multitude of challenges including poverty, poor or no communication network systems, failing road infrastructures, political issues, supply chain delays, crime including kidnapping, violence and poor inventory management. The key points focused on supply chain management include supply chain strengthening, sustainability, proper inventory management and distribution. To date activities that have been introduced as a solution to better inventory management by Reach Out Cameroon have included capacity building of Community Health Workers in medicine management, the provision of inventory management tools and the provision of drug boxes for proper conservation of medication.


MedSource Group Limited, Kenya
MEDSOURCE GROUP is a Kenya based pioneer med-fin-tech. Its mission is to improve access and availability of affordable, quality medications and supplies. The key stakeholders are pharma distributors, importers, manufacturers, vetted private healthcare enterprises and financial inclusion partners. The African pharmaceutical market is rapidly growing and expected to be worth $70 billion by 2030. An influx of counterfeits, limited access to credit, fragmented markets, slow-paced adoption of tech for ease of business and unlicensed outlets and practitioners structural constraints hamper the realisation of universal health coverage aspirations. This presents a window of opportunity to deploy disruptive innovations to address the gaps. As a Group Purchasing Organisation, MedSource leverages on economies of scale aggregating purchases from vetted healthcare enterprises directing them to a select group of pre-vetted manufacturers and distributors. The Enterprise Resource Planning platform enables users to real time access inventory management services and a B2B marketplace. Members can also access working capital solutions via their inventory finance product offering. To date over 5 million patients have been impacted with 50 last mile healthcare businesses supported through inventory financing and availed capacity building to over 1500 professionals.
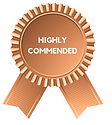
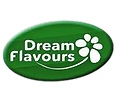
White Angels, TA Dream Flavours
WHITE ANGELS trading as DREAM FLAVOURS is owned by five Batswana Women with a passion for dairy and indigenous fruits. This passion drove them to look for meaningful ways to contribute to their community. They decided to align with the Sustainable Development Goals by buying raw milk from the local farmers to promote Agricultural Value Chain. They then also intentionally created jobs by sourcing wild fruits from unemployed women who gather them from the forests. They realised that the wild fruits of Botswana are given very limited attention and so changing the economic story of their country was a driving ambition for them all. The unique fruits for the yoghurt is pulped which gives it an outstanding taste that reveals the Botswana pride. Their cold chain logistics allows the organisation to supply more than 20 chain stores and 10 hotels and they are gradually expanding into more areas. Their aim is to continually enhance their supply chain excellence and so they consistently improve their performance by evaluating their KPIs such as on time delivery and customer satisfaction.
SUPPLY CHAIN DIGITAL TRANSFORMATION

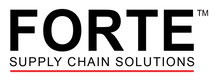
THE LOGISTICS GROUP (TLG) and FORTE.
The Logistics Group (TLG) manages the trans-modal movement of coal from Phalaborwa to the destination at the Port of Maputo, Mozambique with an annual average movement of between 900 > thousand tons annually. This multi-modal approach requires the combined efforts of three of the subsidiaries within TLG namely: The Logistics Company that arranges 3rd party primary transporters from the mine in Phalaborwa to stockpile in Ressano. TLG Mozambique that manages the receipt of bulk stock at Ressano with weighbridge operations and front loaders to transfer the bulk stock from the stockpile on railway wagons. Matalo Cargo Terminal that operates the locomotives with TLG wagons carrying bulk stock from Ressano depot to Maputo port for transfer to the vessel or temporary stockpile in Maputo terminal. Creating a digital twin as a digital representation of the physical movement and process of bulk stock moving from the origin (pit) all the way to the point of discharge (port) to represent its brick-and-mortar counterpart in the real world. To create the digital twin 5 different software applications were integrated, representing two main modes of transport being road and rail. Volume of transactions covering 1 082 682 tons per year with 29 567 truckloads and 44 transporters representing 1400 trucks. The result has shown complete transparency on stock variances with improvement in ratio for stock shortages based on loading vs offloading weight, due to real-time stock visibility. Automated reports to transporters being used and end clients receiving stock. First-time actual track & trace visibility on rail locomotive/wagon movements of stock.


Vector Logistics – Digital Twin Project
The supply chain team proudly introduced and implemented a Transportation Optimization Digital Twin using Alteryx, an analytics process automation tool. This ground-breaking solution automates data pre-processing into Coupa, streamlining transport optimization modelling and enabling rapid response to key business inquiries. By reducing time spent on data pre-processing, the team can focus on the essential insight generating aspects of transport optimization modelling, to lower costs, minimize emissions and drive business value. The Transportation Optimization Digital Twin revolutionises supply chain operations by optimising transport scenarios, analysing fleet mix for optimal vehicle combinations, and implementing Nominated Delivery Day (NDD) smoothing to enhance scheduling efficiency. This innovative solution positions Vector's Supply Chain team as leaders in the digital transformation of the industry, offering cost-effective and sustainable supply chain operations. Vector is excited to showcase their Transportation Optimization Digital Twin in the Digital Transformation category, confident in its ability to drive financial transformation and enhance supply chain efficiency.

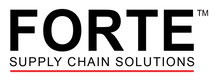
PepsiCo and Forte Supply Chain Solutions
PEPSICO’s primary transport division required a central platform to display its logistical planning from each respective transporter and the ability to share this real-time load status and detail with the relevant clients or senders/receivers of the cargo. The different departments impacted at PEPSICO logistics department, to achieve this single source of data insight are mainly the expeditors, planners and sales departments. 55 different transporters based nationally – representing around 1500 vehicles included in the project for data contribution. 4000 – 5000 consignments per month that require expediting from PEPSICO. Representing over 1500 different SKUs within the daily consignments to be tracked via expeditors on FLOW Platform. The data required to be shared via a live feed of each primary transporter's data source is load status, current position and notifications and or exceptions. Importantly with emphasis not to create additional workload in terms of data upload for the relevant transporters, different options were created and presented to the transporters for sharing data: integration with their respective transport software, sync a manual sheet (like excel) or capture the data with user defined login in FLOW Platform. Mitigating the process impact or cost to transporters and ensuring PEPSICO stays true to its digitization strategy to remain competitive within all sectors of the business.
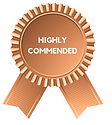
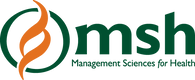
Management Sciences for Health
MSH in Kenya on strengthening supply chain systems for improved access to non-communicable diseases (NCDs), health products and technologies. The Blue Print project funded by Takeda Pharmaceuticals. There is growing support in countries to expand Universal Health Coverage (UHC) to increase access to NCD services and Medicines at the primary level. The Global NCD action Plan (GAP) has set a goal of 80% availability of the affordable basic technologies and essential medicines, including generics by 2025 to treat NCDs. Evidence from research indicates that there are substantial barriers to equitable access to essential medicines and basic health technologies for NCDs. It has been found that the rational use of medicines can considerably reduce the burden of NCDs in many countries. Despite this reality, essential medicines have remained unavailable in the public sector and often unaffordable in the private sector of many countries, especially low- and middle-income countries. In Kenya, through the optimization of NCD Health Products and Technologies information management systems to improve data visibility, availability, accessibility, and utilization across the entire NCD HPT supply chain will lead to enhanced transparency and accountability across the NCD HPT supply chain.


LIVEFR8
LIVE FR8 is honored to introduce a revolution in the road freight logistics industry. With supply chain management becoming increasingly complex, the LIVE FR8 solution streamlines freight operations simply, securely and at low cost. “Ruggedised” for the African environment, LIVE FR8 connects all categories of shippers, carriers, and brokers in real-time, creating a dynamic ecosystem for road freight transportation. Its cloud application simply finds and manages shipments, ensuring efficiency and certainty. Key features include free exposure of loads and transporters, searchable by geolocation, reducing empty trips and minimising environmental impact through reduced emissions. LIVE FR8’s app provides real-time visibility into the entire transportation process, enabling stakeholders to track shipments, manage subordinates and documentation, and communicate effectively. Supplier and carrier ratings assure trustworthiness and accountability among all parties and improve customer satisfaction. LIVE FR8’s platform also offers data analytics, billing and reporting capabilities, empowering businesses to gain valuable insights into their supply chains so they can make data-driven decisions, identify bottlenecks, and continuously improve their logistics operations.
EXCELLENCE IN TRANSPORT AWARD

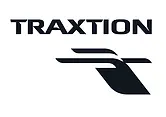
TRAXTION - Calabash Project
Calabash Freight Rail Limited started operating on the Tanzania Zambia Railway Authority (TAZARA) railway line under the Calabash Freight rail access agreement after it was opened to private operators IN 2018. Calabash is a strategic joint venture between Calabash Freight Ltd and Traxtion. The TAZARA line is an important route for copper exports from Zambia and the DRC and this joint venture was ideally positioned to take advantage of the opportunity due to Calabash Freight Ltd’s extensive knowledge on the region and operational requirements while Traxtion provided best-in-class assets and technical knowledge. In the 2018/19 financial year, Calabash accounted for more than 50% of the freight volumes transported on the TAZARA line, with overall volumes increasing by 60% year-on-year. About 466 trains have travelled along almost 2000 km of rail to arrive safely at their final destinations. More than 600 000 metric tonnes have been transported with seamless reliability on the TAZARA line. The success story on the TAZARA rail network is a result of reliable locomotives, a dedicated technical team and a highly skilled operational team, supported by Traxtion’s Rail Services Hub in Rosslyn, Pretoria, South Africa.
SUPPLY CHAIN REENGINEERING


UNION COATINGS INC
Union Coatings Egypt is a leading company in coating production that aimed to improve and enhance its supply chain by using the APICS SCOR model. They faced many challenges such as but not limited to lead time, inventory management, variability in orders, logistics costs, and broken ERP. By using this model they were able to re-engineer and transform their immature MTS supply chain, into a more developed resilient MTO and ETO supply chains. Through this development, Union Coatings was able to achieve its goals, decreasing the delivery lead time from 15 days to 24 hours, increasing OTIF from 40% to 70%, and overall equipment effectiveness increased by 20%. Applying the SCOR model also helped Union Coatings to raise sales volume by 30%, reduce the Cash Conversion Cycle from 180 to 60 days and increase Union Coating’s Global presence through an agile business model. Union coating was looking forward to having an agile and highly responsive supply chain, transforming to “ETO” (engineer-to-order) and “MTO” (make-to-order) instead of “MTS” (Make-to-Stock), and decreasing planning delivery lead time. By using the SCOR model, Union coating was able to overcome more of the challenges they had such as Customer returns, Materials planning and air freight cost, Materials availability and overstock, and lead time Calculation. They were able to boast a successful year where they saw instrumental changes in their supply chain and culture, translating into a global success, and gaining trust from international customers in Europe and Canada, resulting in a new factory opened overseas, widening their array of customers.